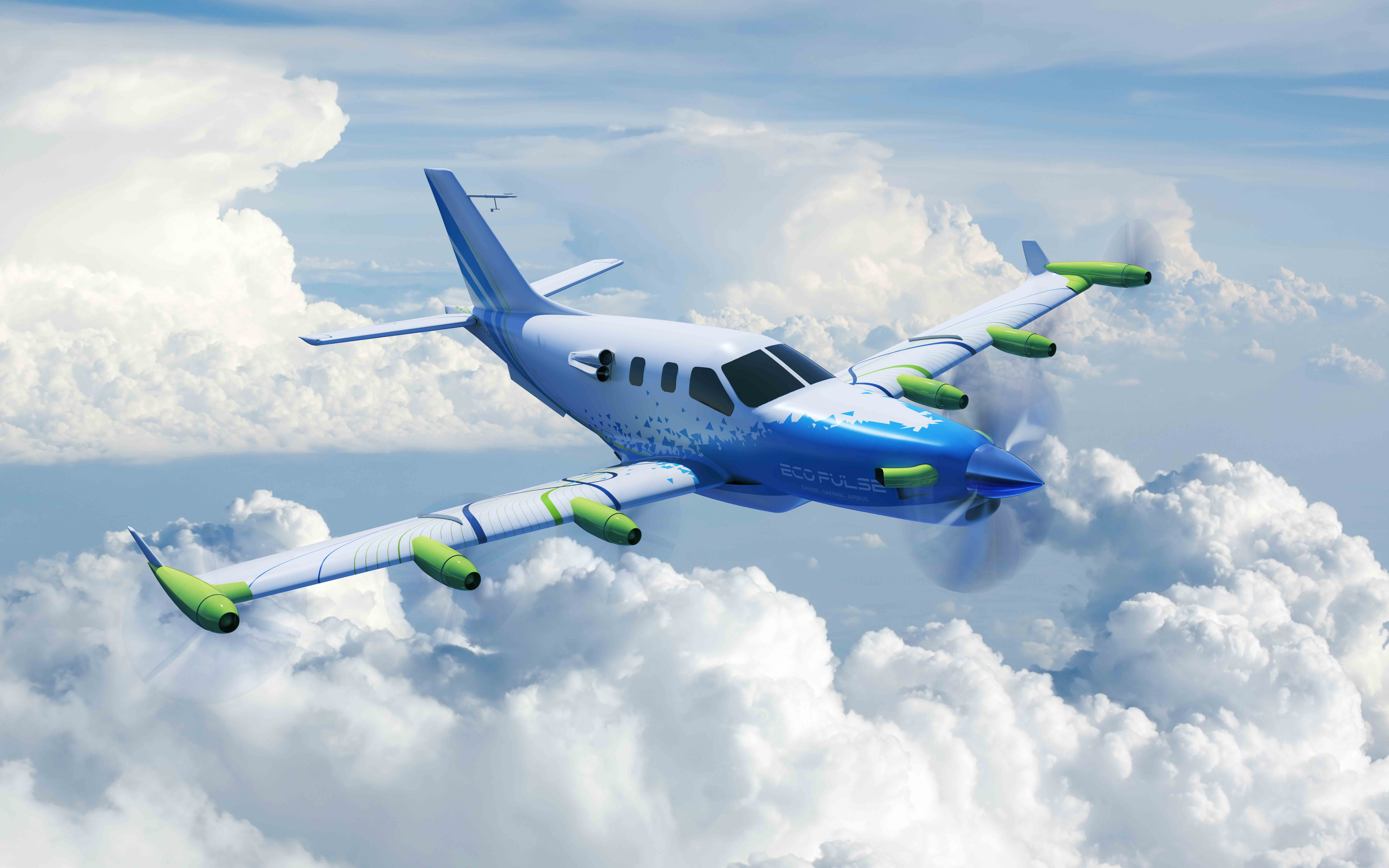
Tarbes, France, December 10, 2020 – The EcoPulse™ distributed propulsion hybrid aircraft demonstrator – which is being developed by Daher, Safran and Airbus with the support of France’s CORAC civil aviation research council – has successfully passed its Preliminary Design Review as a first key step toward validating the project’s feasibility and firming up the architecture for a first flight scheduled in 2022.
Incorporating a distributed propulsion configuration from Daher, Safran and Airbus, this shared hybrid aircraft project has the goal of helping to transform the aviation sector. EcoPulse™, which was unveiled at the 2019 Paris Air Show, is backed by the French government – with a reaffirmation of support coming in the framework of France’s recovery plan presented last June.
By laying the framework for light aircraft by the end of the decade, it will allow the development of technologies that reduce the environmental footprint of future commercial aircraft, thus contributing to the air transportation sector’s decarbonization objectives by 2050.
After more than one year of development based on a light aircraft platform supplied by Daher, the project has reached a key milestone with the successful completion of its Preliminary Design Review (PDR), which enabled the validation and freezing of the demonstrator’s baseline configuration, as well as confirming the hybrid distributed propulsion system’s level of safety and compatibility with the aircraft.
The project is now entering the assembly and integration phase at Daher, with systems supplied by Safran and Airbus.
Daher to begin the demonstrator’s assembly in 2021
In carrying out its responsibilities for installing components and systems, flight testing, global analysis and airworthiness, Daher has adapted its demonstrator aircraft platform to ensure the integration and compatibility of a hybrid system with distributed propulsion at the necessary safety level.
The Preliminary Design Review’s successful completion enables Daher to begin the demonstrator’s assembly phase at its Tarbes, France site, where the initial components were designed and delivered. The start of final assembly is planned for late 2021, with the first flight scheduled to take place in 2022.
“With this demonstrator, Daher intends to develop the key architectural principles for future hybrid aircraft. The project reaffirms our commitment, as a general aviation manufacturer with our Kodiak & TBM product lines, to more efficient and eco-responsible aviation. This is reflected by our company’s active participation in numerous ambitious collaborative research projects aimed at decarbonizing air traffic.”
Pascal Laguerre, Daher’s Chief Technology Officer
The electric thruster configuration is validated by Safran
Safran, which is responsible for EcoPulse’s distributed hybrid-electric propulsion system, has finalized the technical configuration of its six electric thrusters. They will be fitted with 50 kW ENGINeUS™ electric motors with integrated electronics and patented air cooling, as well as propellers supplied by DUC Hélices. The Safran ENGINeUS™ motor will be submitted for EASA certification – the same type as granted for a turboshaft engine.
Also validated by Safran are the installation interfaces for the propulsion system’s other components, along with the power management system, the turbogenerator and the high-voltage wiring that will supply electrical power to the thrusters. The turbogenerator, which performed its first test bench runs in 2018, will soon undergo additional tests.
The next step for Safran will be its delivery of an initial electric thruster to Airbus for wind tunnel and endurance testing, in preparation for qualification of the thrusters’ use on EcoPulse’s first flight.
“EcoPulse is an ambitious project, and designing hybrid propulsion on this new aircraft architecture is a key skill that Safran is proud to master. Mobility needs are changing, and the Group is responding to them by offering advanced and sustainable technologies that have taken shape with this important milestone reached today.”
Stéphane Cueille, Senior Executive Vice President and Chief Technology Officer, Research & Technology and Innovation at Safran.
Airbus wind tunnel testing of the electric motor, propeller and nacelle
Completion of the EcoPulse preliminary design review enables Airbus – currently involved in the demonstrator aircraft’s aerodynamic modeling – to schedule the start of wind tunnel testing for propeller/nacelle assembly during the first quarter of 2021. The electric engine, supplied by Safran, will be tested as well. The results of these tests will enable the identification of the propeller’s performance characteristics when associated with an electric engine, and validate the engine cooling process.
In addition to these wind tunnel tests, Airbus also is planning to simulate the nacelle’s aerodynamic behavior.
“The EcoPulse demonstrator program, initiated by CORAC with the support of the French DGAC civil aviation agency, is an important step in our ambition to decarbonize the aeronautical industry. It will allow us to study how distributed hybrid propulsion could be integrated into the aircraft of tomorrow and significantly reduce their environmental impact.”
Jean-Brice Dumont, Executive Vice President Engineering, Airbus