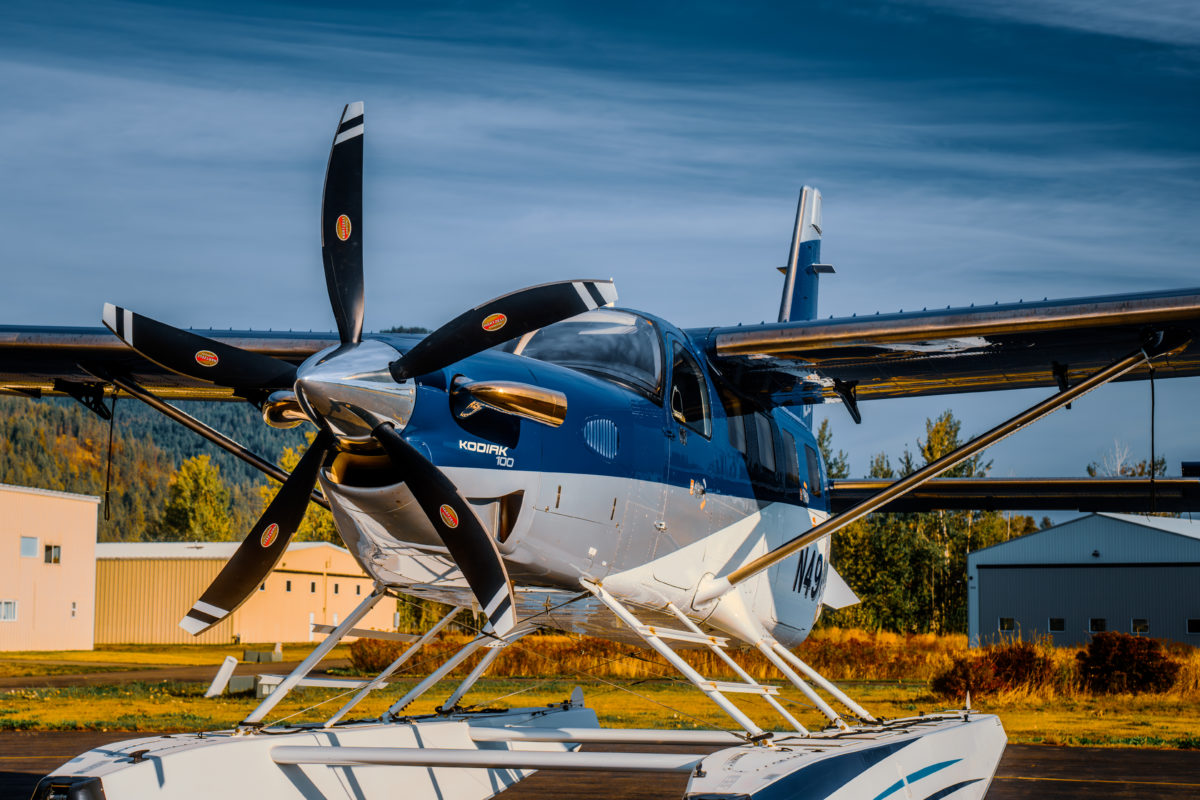
Daher today announced the latest enhancement to its Kodiak 100 aircraft by integrating Hartzell Propeller’s five-blade composite propeller with a pitch latch function for water operations on floats.
The five-blade propeller for Kodiak 100s was introduced by Daher in 2023, and its new pitch latch function enables float-equipped aircraft to be easily maneuvered on water with greater control and safety because the propeller can be set in a fine pitch position during engine startup and shutdown.
“This marks another improvement for our multi-role Kodiak aircraft family, which is increasingly in demand by government agencies, commercial operators and private owners,” explained Nicolas Chabbert, CEO of Daher Aircraft, when announcing the new feature at the National Business Aviation Association’s Business Aviation Convention & Exhibition (NBAA-BACE) in Las Vegas, Nevada.
All Kodiak 100s are delivered from Daher’s Sandpoint, Idaho factory with the structural and operational enhancements for water operations – including the capability of being equipped with Aerocet floats, along with the application of a special skin gap fillet sealant for enhanced corrosion protection in high salinity environments, as well as designed-in structural reinforcements necessary to support the unique loads associated with water landings.
In addition to the five-blade propeller’s availability with pitch latch function on new-production Kodiak 100s, the composite propeller can be retrofitted on in-service Kodiak 100s via the Hartzell Top Prop program.
Tailored specifically for use on Kodiak 100s, this five-blade composite propeller incorporates Hartzell’s lightweight Raptor propeller hub technology. In addition to being 13 lbs. lighter than the four-blade metal propeller, the new five-blade version reduces the Kodiak 100s ground takeoff roll by six percent at maximum gross weight. Additionally, the propeller is durable by design, with a TBO (time between overhaul) of 4,000 hours/six years, and an industry-leading warranty of six years or up to 4,000 hours.
Among the composite propeller blades’ key features are the durable nickel-cobalt leading edge, a nickel erosion screen for FOD (foreign object debris) protection, urethane paint for improved erosion protection, and the use of aerospace-grade carbon fiber.
The Kodiak 100’s five-blade propeller also is 6.6 dB quieter, turning at 2,000 rpm for a maximum torque – which is 200 rpm slower than the four-blade metal propeller, providing an operational advantage in noise-sensitive areas. This slower rotation speed reduces vibration aboard the aircraft as well, and lowers the Kodiak 100’s flyover noise to well within the European EASA airworthiness authority’s stringent 78 dB(A) requirement. At a diameter of 96 inches, the five-blade composite propeller has a ground clearance of 20 inches when the Kodiak 100 is equipped with floats.
Introduced by Daher in 2021, the Kodiak 100 Series III version currently in production is the third generation of the turboprop-powered Kodiak 100 aircraft family. It incorporates enhancements and standard features for improved flight safety, greater cabin comfort, augmented operational capabilities from both unimproved strips and on water with floats, as well as upgraded quality and more comprehensive maintenance coverage.
Flight safety-related upgrades include the integration of Garmin’s GWX 75 Doppler-capable, fully stabilized color weather radar with a high-definition color palette that enables more detailed contouring of storm cells. This is in addition to such standard equipment as Garmin’s G1000 NXi fully-integrated flight deck, the GFC700 autopilot with full envelope protection and level mode, an angle of attack (AOA) indicator, SurfaceWatch runway monitoring technology, ChartView-enabled card and the Synthetic Vision Technology for virtual flight reference.
Kodiak 100 Series III aircraft qualify for Daher’s four-year Kodiak Care maintenance program, which covers scheduled maintenance up to the fourth annual inspection or a total flight time of 1,000 hours – whichever comes first. Also included is Pratt & Whitney Canada’s Gold-level ESP Maintenance Program for the PT6A-34 turboprop engine, along with one year of CAMP Systems’ maintenance tracking and a one-year subscription for Garmin’s NavData electronic database.
In addition to the Hartzell five-blade composite propeller’s integration on the Kodiak 100, five-blade composite propellers from Hartzell are utilized on Daher’s other in-production turboprop-powered aircraft: the Kodiak 900 and the TBM 960/TBM 910.