By Dominique Bailly, Director of R&D, Daher
As published in JEC Composites Magazine N°159 – November – December 2024 – jeccomposites.com
Until recently, the production of composite aeronautical parts was more of an artisanal process than a truly industrial one. The main reasons were highly manual processes and lengthy, energy-intensive curing times. However, R&D efforts over the years are paving the way for the production of more complex parts at higher rates.
The latest generation of aircraft has introduced a new class of composites, including thermoplastic composites, which can be produced more quickly using less energy-intensive processes and are capable of meeting higher production rates. Currently, their use remains limited to small, non-critical and lightly loaded parts. Daher’s Nantes factory (Figure 1) has specialised in producing thermoplastic aeronautical components using a highly automated process that supports high production rates. Among the 300,000 parts produced annually by the factory’s automated production lines are mostly small ribs, nearly a thousand types of clips, floor structure components and covers for major aerospace programs.
Thermosets or thermoplastics?
In contrast to these thermoplastic composites, thermosetting composites, which are more mature, hold a dominant position in the aerospace market. They are used in programs such as the A320, A340, A350, A380 and B787. Thermosets enable the creation of complex geometries and structures while remaining relatively easy to implement. However, the lack of automation and the long curing times (approximately 8 hours) make them unsuitable for high production rates. Nevertheless, a new generation of “fast cure” thermosetting composites is currently in development, which will significantly reduce production times.
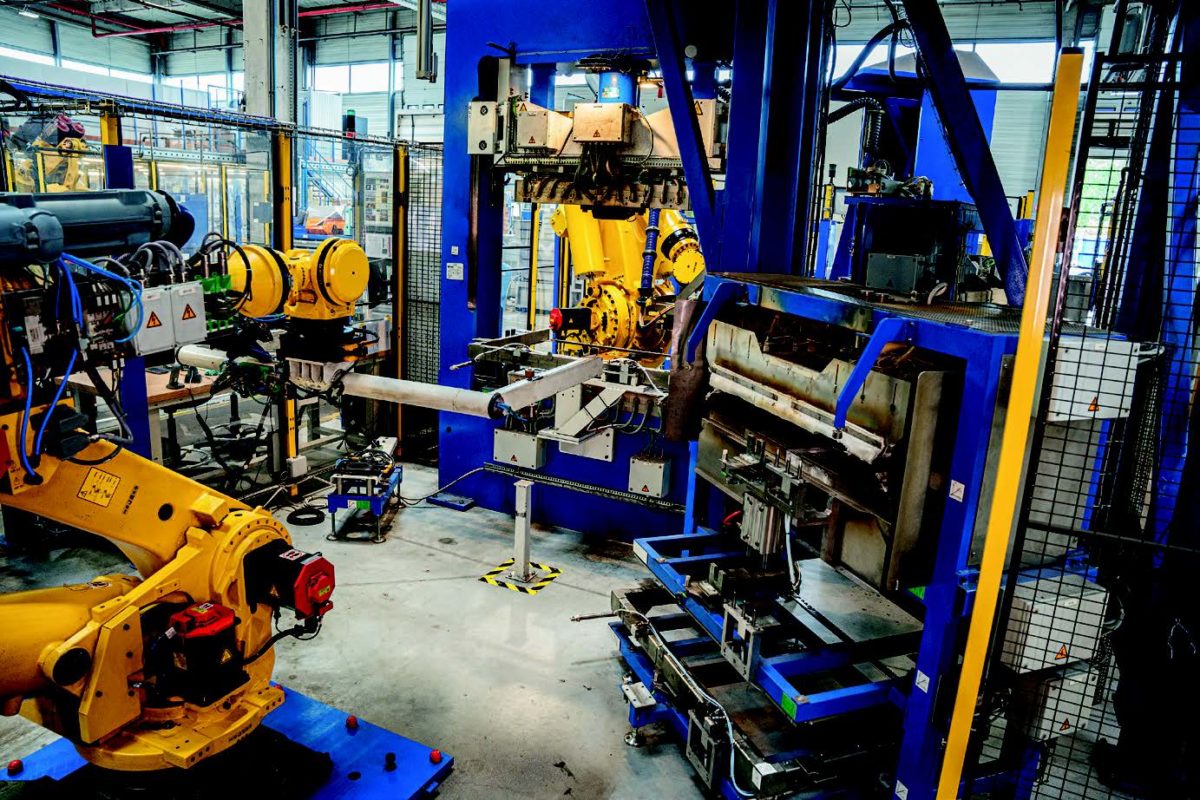
Depending on the design and production requirements of the parts, Daher, a tier 1 supplier to the aerospace industry, offers either thermosetting or thermoplastic composites. The goal is to bring the right chemistry to the right place, depending on the loads, environmental conditions, shape and function of the part. Essentially, the challenge is to balance the benefits of both technologies to offer the best compromise for each specific need.
While still in the minority for existing aerospace programs, thermoplastics offer numerous advantages that position them as essential materials for the next generation of aircraft. Unlike epoxy resins, which harden permanently once polymerised, thermoplastics can be reheated and reshaped, allowing defective parts to be reworked. Moreover, thermoplastic components are highly recyclable. Their production management is also easier and less energy-intensive since they do not require freezers for storage, clean rooms or climate-controlled environments, and there are no expiration concerns. Thermoplastic composites also benefit from a much shorter heating and forming process than thermosets, allowing production units to increase output. Finally, thermoplastic parts can be assembled by welding, eliminating the weakening and weight increase caused by drilling and the use of expensive riveted assemblies.
Mass savings, weldability, reparability, recyclability… thermoplastic composites offer many advantages. Moreover, they require far less tooling than thermosetting composites to achieve the same production rates. Today, thermoplastic composite parts are flying on the Rafale, as well as the Airbus A340, A350, A380, A400M and some business jets (notably Gulfstream and Dassault).
Significant R&D Efforts
To harness this potential, Daher has been conducting extensive Research and Development (R&D) over the past decade, focusing both on the composites themselves and the associated manu- facturing processes. The goal is to reach the necessary maturity level to produce complex and/or large parts for the next generation of commercial aircraft.
Primarily centred on thermoplastics, particularly PolyEther Ether Ketone (PEEK) and LMPAEK resins, this work has resulted in demonstrators of large, thick or variably thick wing parts, as well as engine environ- ment components like air intake bulkhead, Rear Secondary Structure (RSS), Forward Secondary Structure (FSS), pylons, etc. Developing automated processes capable of producing self-reinforced composite structures with low mass and high stiffness is one of the top priorities in Daher’s research efforts.
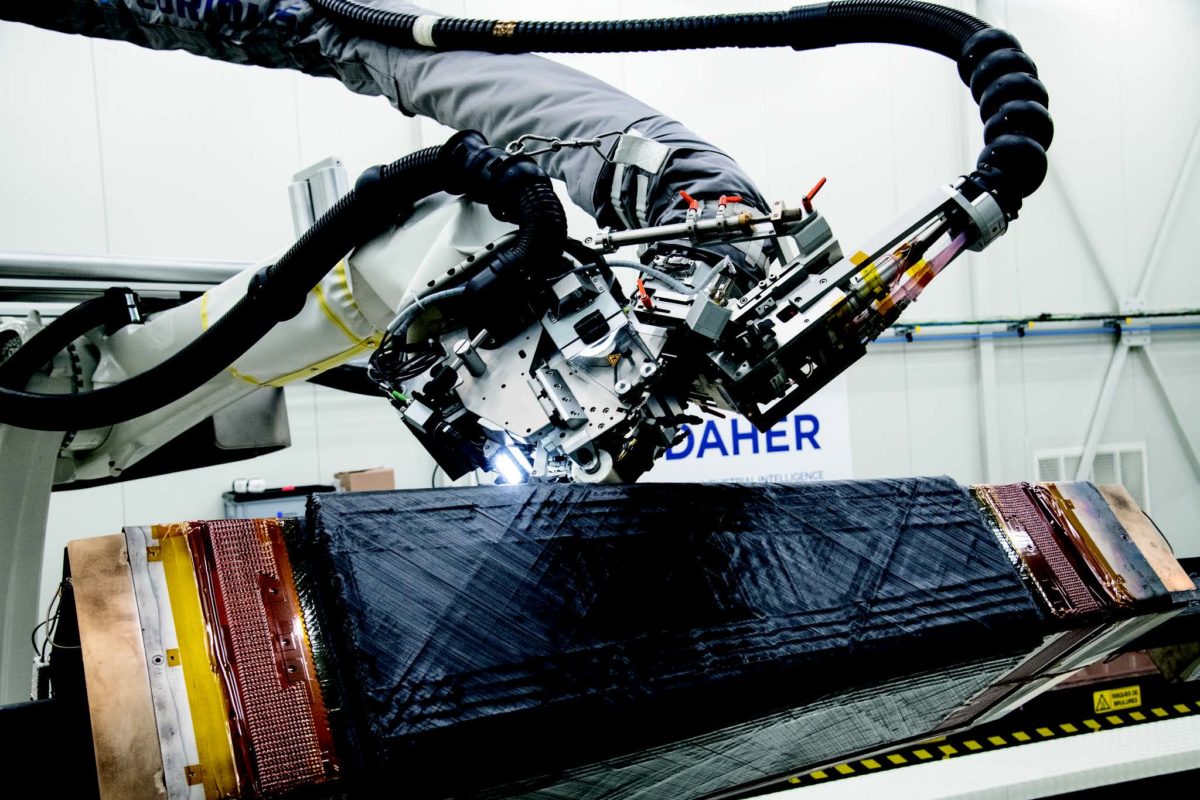
In addition to thermoplastic welding, which is particularly suited to high production rates and significantly reduces weight by eliminating rivets, another patented process—direct stamping—allows several manufacturing steps to be bypassed, accelerating production cycles while reducing energy consumption and production costs. This process, combined with Automated Fiber Placement (AFP), which Daher is among the first to master at the appropriate level, enables the production of large, complex and thick thermoplastic parts.
Among the parts made using this technology is the air intake frame of an engine demonstrator developed in partnership with Airbus. With a circumference of several metres, this part, made up of 4 assembled sections, is one of the largest ever produced in thermoplastic. Another example is a thick (around 35mm) engine suspension pylon produced as part of the MATCH project by IRT Jules Verne, made possible by AFP (Figure 2), resulting in significant weight reduction.
For thermosetting composites, a similar process exists on the market, but its compatibility with new “fast cure” resins has yet to be validated.
Other thermoplastic aerospace parts have been made by Daher as part of research projects in partnership. Among them is a fully thermoplastic version of a TBM aircraft’s horizontal stabiliser, presented at JEC World 2024. As part of the Trampoline project supported by the French Directo- rate General for Civil Aviation (DGAC), this large part was produced using AFP and direct stamping technologies, then assembled by thermoplastic welding rather than riveting. It demonstrates what future wing components of tomorrow’s aircraft might look like, with clear advantages in terms of weight, performance and recyclability.
In addition to its progress on thermoplastics, Daher continues to work on thermosetting composites, following its dual objective of eco-design and increasing production rates. Daher is developing a compression moulding process which, combined with new fast-cure resins, will address high production rates while limiting material use.
From R&D to industrialisation
In parallel with its R&D programs, Daher has invested in the industrialisation of production processes. Carried out at Daher’s Nantes plant with support from the Pays de la Loire region, the ODDICEA project laid the groundwork for the connected factory of the future by working on the connectivity of industrial resources and the integration of production line data into a centralised Manufacturing Execution System (MES). The second phase of this project, currently underway, aims to leverage this data to provide benefits in terms of energy savings and production optimisation.
A stamping cell is also under consideration, which would allow the production of large and thick parts at a rate sufficient to supply 70 to 100 aeroplanes per month. Furthermore, work has already begun with LIST on high-speed infrared welding for thermoplastic parts.
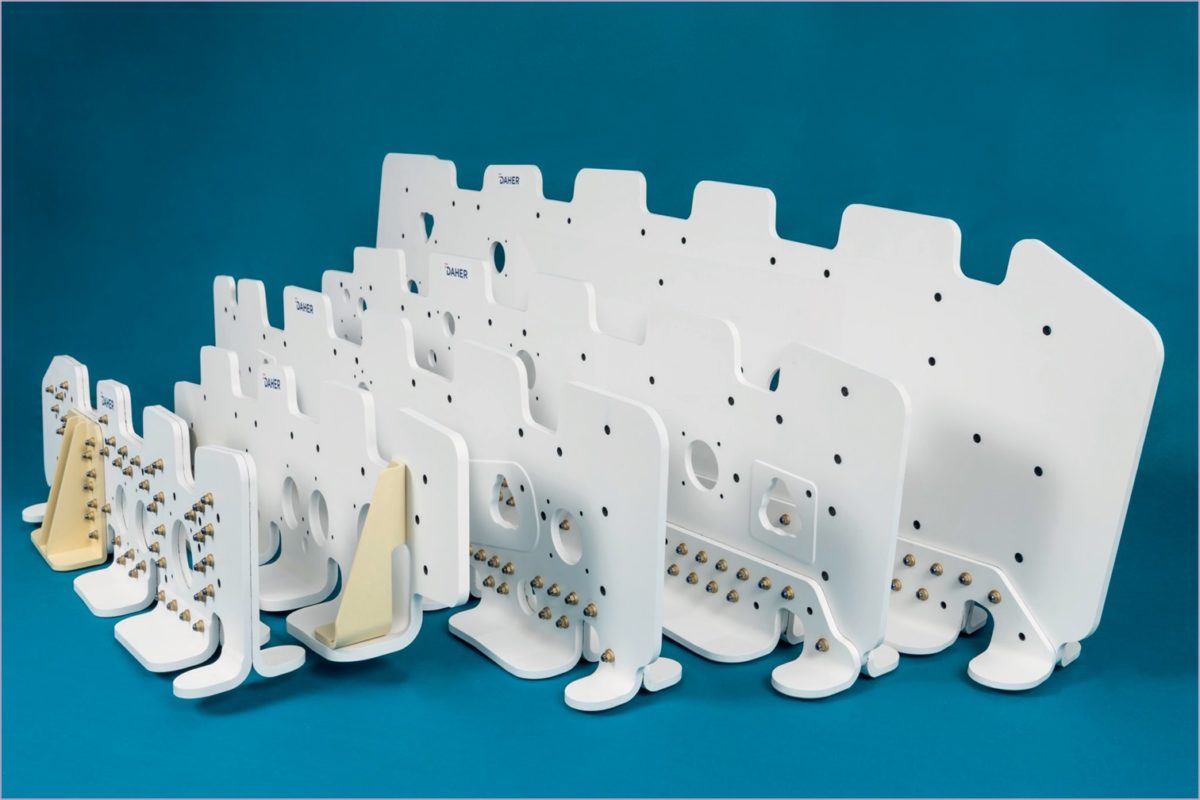
What parts for tomorrow’s aircraft?
These various developments, both in terms of R&D and the industrialisation of production, suggest the industrial production of aeronautical parts suitable for a wide range of uses, balancing production rate, productivity and cost optimisation. Energy savings associated with the production of thermoplastic parts, along with reduced raw material usage and recyclability, also support eco-design efforts and, more broadly, the Corporate Social Responsibility (CSR) agendas of industry players. The ultimate goal is to be ready to offer innovative aircraft parts (Figure 3) with proven characteristics and capabilities, as well as the corresponding industrial means when the 2 major commercial aircraft manufacturers launch their new programs. Daher aims to leverage its expertise in different categories of composite materials to strengthen its position as a leading supplier.