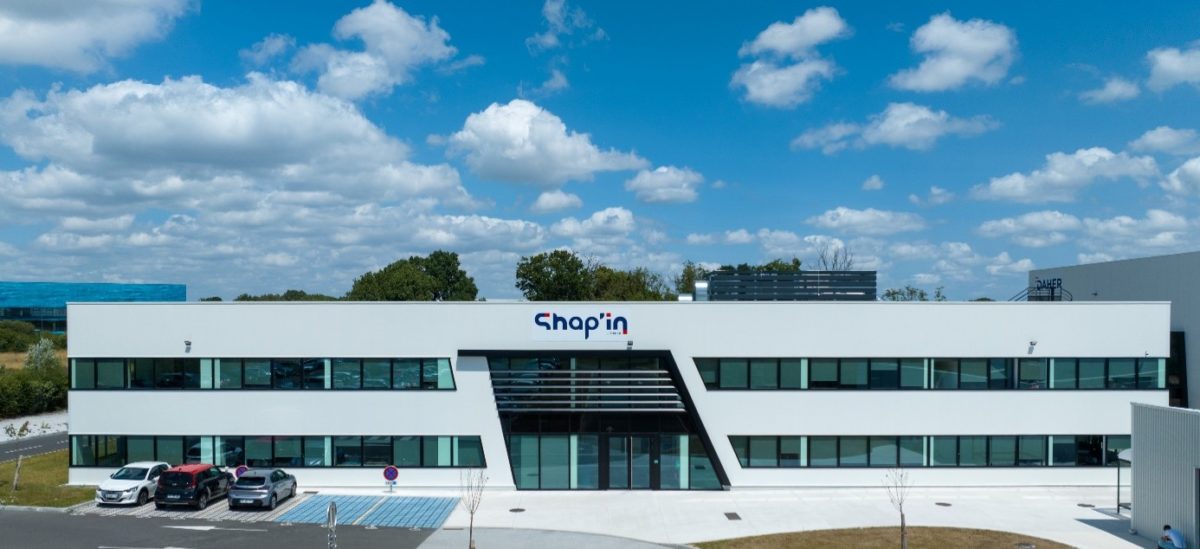
Daher is celebrating the second anniversary of Shap’in, its technology center dedicated to the composite aerostructures of the future, which is located at the company’s Saint-Aignan-de-Grandlieu site near Nantes, France.
Designed to centralize R&D and accelerate the maturity of composites, Shap’in takes a new step by moving towards their industrial scaling. This transition is a key milestone for Daher, which aims to play a major role in tomorrow’s large aerospace programs where these materials will be crucial.
Toward the progressive industrialization of composites
With Shap’in, Daher is laying the foundations for the progressive industrialization of composites, combining innovation and sustainability. With these advancements, the group is accelerating the maturity of composites and their gradual integration into its factories. This dynamic will enable Daher to meet the growing demands of aerospace for the future.
Structuring the maturity of composites
To achieve this ambition, Shap’in has spent two years developing solutions in automation, connectivity, and flow optimization – integrating the imperatives of competitiveness and decarbonization. In direct connection with Daher’s factories in the region, these processes are being tested and optimized for gradual deployment, initiating a ramp-up that will continue in the coming years.
A collaborative ecosystem to accelerate innovation
This transformation dynamic relies on open collaboration, supported by such French funding sources as CORAC (the Council for Civil Aeronautical Research), the French government, and the region in which Shap’in is located.
Situated at the heart of regional innovation, the Daher Shap’in tech center collaborates with startups, SMEs (small and medium enterprises), aircraft manufacturers, academia, and the IRT Jules Verne to explore new processes, test cutting-edge materials, and optimize composite manufacturing. These partnerships enable a faster transition from research to industrialization, relying on a network of expertise and advanced technological resources.
Thermoplastic composite welding: a technological breakthrough
Among these advancements, fastener-free assembly represents a major technological breakthrough, allowing for a reduction in the weight of aerostructures by up to 15% – a gain impossible with traditional methods. Following its acquisition of the Dutch company KVE in 2019, Daher developed a patented induction thermoplastic welding technology. Last November, this innovation was validated at Shap’in with a fixed horizontal tailplane demonstrator for aircraft, confirming its industrial feasibility for the first time.
“Shap’in is the culmination of our ambitions in composite innovation and industrialization. The validation of thermoplastic welding is a real example of our ability to transform a technological breakthrough into an industrial solution. This breakthrough paves the way for a new generation of lighter and more efficient aerostructures, adapted to the requirements of future aircraft.”
Dominique Bailly, R&D Director and Head of Shap’in at Daher
A structured recycling model for composites
Beyond advancements in assembly, Shap’in also is rethinking the entire lifecycle of composite materials. In partnership with Daher’s Saint-Aignan factory, the tech center has implemented a structured recycling process in three stages:
- Sorting and the collection of waste;
- Grinding and transformation into pellets;
- Reuse for the production of new parts.
This process has been applied to replacing the pilot’s rudder pedals of Daher’s TBM aircraft – which were historically made of aluminum – with pedals made from recycled composite materials. Approved by European authorities, they will be integrated into production starting in 2025.
Heavy thickness machining: a differentiating capability
To meet the most critical applications, Shap’in also has enhanced its expertise in composite machining. Thanks to a heavy-thickness machining machine funded by the French government under the “France Relance” program, Daher can now machine composite parts up to more than two centimeters thick. By mastering these processes, Daher has joined the select group of industrial players capable of addressing these markets.
With Shap’in, Daher has reached a milestone in its industrial ramp-up. The ability to machine heavy-thickness composites opens access to markets where only a few global players are present.
Eco-responsibility at the heart of innovation
“The more eco-responsible aviation of tomorrow will rely on these innovative processes and materials, and we have been preparing to meet this shift for more than 10 years. Respect for the environment is at the heart of our technological roadmap. Early on, Daher identified advanced composites as a true catalyst – a ‘game changer’ addressing the major challenges of performance, weight reduction, and production rates for aircraft manufacturers. With Shap’in, we are accelerating the efforts to decarbonize our products throughout their lifecycle, from eco-design to the circular economy, with optimal management of the recycling of our production waste. We are convinced this approach represents a decisive asset for the entire industry.”
Julie de Cevins, Chief Sustainability Officer at Daher